- Home
- Business Optimization
- Solutions
- Equipment Management
- Digital asset management for project managers
DIGITAL ASSET MANAGEMENT FOR CONSTRUCTION PROJECT AND JOBSITE MANAGERS
How to rapidly boost productivity, safety and on-site organisation
As a project or jobsite manager, it’s a daily logistical challenge to make your construction sites efficient, safe and productive – and highly rewarding when you succeed.
You need to plan which tools and equipment are needed each day, then make sure they are in the right place at the right time. When the required items arrive on-site, you have to keep track of them and prevent loss or damage.
You also have to comply with ever-complex health and safety regulations. From making sure that workers have current training to knowing that equipment inspection and testing intervals are being adhered to, yours is a job that needs the most efficient asset management system available.
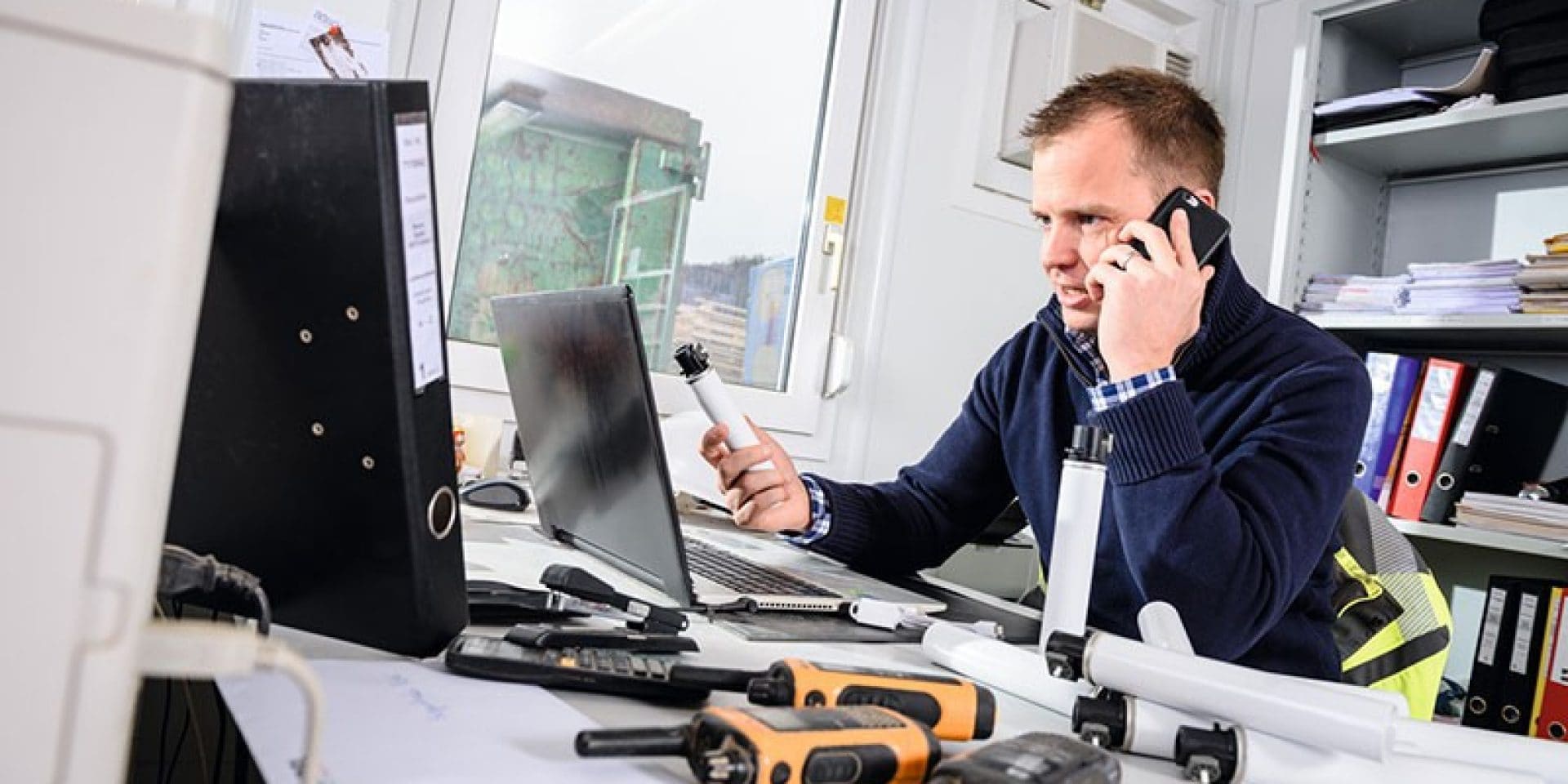
Lack of asset visibility can be costly to many firms
Kevin Hill
Yard Manager, Sonic Rail Services
Although construction is an increasingly hi-tech industry, the way many firms manage projects is far behind the times.
It’s because construction is the second least digitised sector after agriculture. Instead of making use of integrated, digital systems to manage their assets, many firms expect managers to use a patchwork of paper-based systems and simple software like Excel spreadsheets.
It’s a wasteful way of working and it puts needless pressure on you. Why should the average construction firm spend 90 hours each month searching for assets across sites? And why do they rent unnecessary equipment when existing items would be available – if only they were properly tracked. Adding up all these process and administration costs can needlessly cost a company up to $200,000 per year.
If costs and delays like these affect you, you can also end up shouldering the blame – when it’s really your asset management system that’s at fault.
The same thing can happen if you manage administrative assets. If you need to make sure that Health & Safety certificates and clearances are current, that workers have up-to-date training and certification, or have to get equipment tested and inspected at the correct intervals, then you need a system that works with you – not against you.
Trying to do this with a largely paper-based system means essential tasks can easily slip through the net. When this occurs, it can lead to wasted time, unsafe working practices and fines for non-compliance with Health & Safety regulations.
So how can using a digitised asset management system help you avoid these pain points and make the way you work faster, more efficient and safer?
Switching to digital asset management
Samuel Blakeman
Estimator, Blakeman Steel
In terms of cost, time savings and increased efficiency, a switch to digital asset management is a no-brainer for any construction company.
Digital asset management software is increasingly easy to use and relatively cheap to implement. Importantly, cloud based platforms now keep your data more securely than ever. With the right choice of software and intelligent implementation it will quickly cut expenditure on physical assets, free up staff time for more productive purposes, eliminate delays on site and reduce the likelihood of fines by accidentally failing to comply with regulations.
In short, as a project or jobsite manager, your job becomes simpler, more efficient, more cost effective and – above all – more enjoyable.
Benefits of digital asset management
After switching from paper-based administration, you and your colleagues gain access to a digital asset management system via a handset, smartphone or a cloud app within your web browser.
All tools and equipment are being tracked with robust tags, allowing you to see where any item is at any given time, and who is responsible for it. Each item is also assigned to a cost centre, allowing you to identify which parts of your business are most affected by lost or missing items.
Scenario – assigning tools to a jobsite
Assume that you need to make sure that two rotating lasers, a concrete pump, six angle grinders and three drills are at a jobsite tomorrow morning.
Because each item has a rugged tag, which has been scanned into the asset management system using a smartphone, you can log in and see exactly where each item is – whether in the warehouse, on-site, or at a different jobsite. You can also see who is responsible for each item and whether they are available for use the next day.
You can now assign the needed items to a responsible employee, to ensure he gets the equipment to the correct site the next day.
The benefits of doing this are significant.
- Time. You don’t need to spend hours tracking down items using paper-based systems and phone calls. You know the items will be on-site the next day, so you don’t lose time to delays or getting supervisors or other staff involved in tracking items down. Assigning items also takes moments rather than hours.
- Cost. Now that you know the correct equipment is available, you don’t need to buy or lease duplicate items, helping to keep your cost within budget. Because the system tracks the usage of consumables (such as bolts, nails and plasterboard), you can order in the amounts you need – meaning you avoid hoarding and don’t pay for extra assets that you don’t require.
- Fewer lost or stolen items. Because each item is tracked to a location and a responsible person, it encourages workers to take more care of their tools. This leads to fewer lost or stolen items and helps you keep within budgets.
- Full visibility and reporting. You can use system data to benchmark the different jobsites you are responsible for. If one site is using significantly more consumables or losing more tools than a comparable site, system reports can show you. This allows you to investigate problems and set achievable targets tailored to individual sites, based on real-world data.
The time and cost savings you can make using digital asset management are significant. Our work with construction companies has allowed us to identify savings like the following.
- A company spends 15 hours per day (3,600 hours per year) across all of its jobsites searching for and allocating assets at a cost of $162,000 per year. Digital asset management can cut this time at least in half, saving 1800 hours and $81,000 per year.
- A firm makes 10 redundant purchases per month, at an average cost of $500, because of a lack of transparency and employees ‘hoarding’ assets. Digital asset management cuts these costs by 75%, bringing the bill down from $60,000 to $15,000 per year.
A construction company’s four main costs are:
- Labor
- Material & Consumables
- Tools and Equipment
- Subcontractors
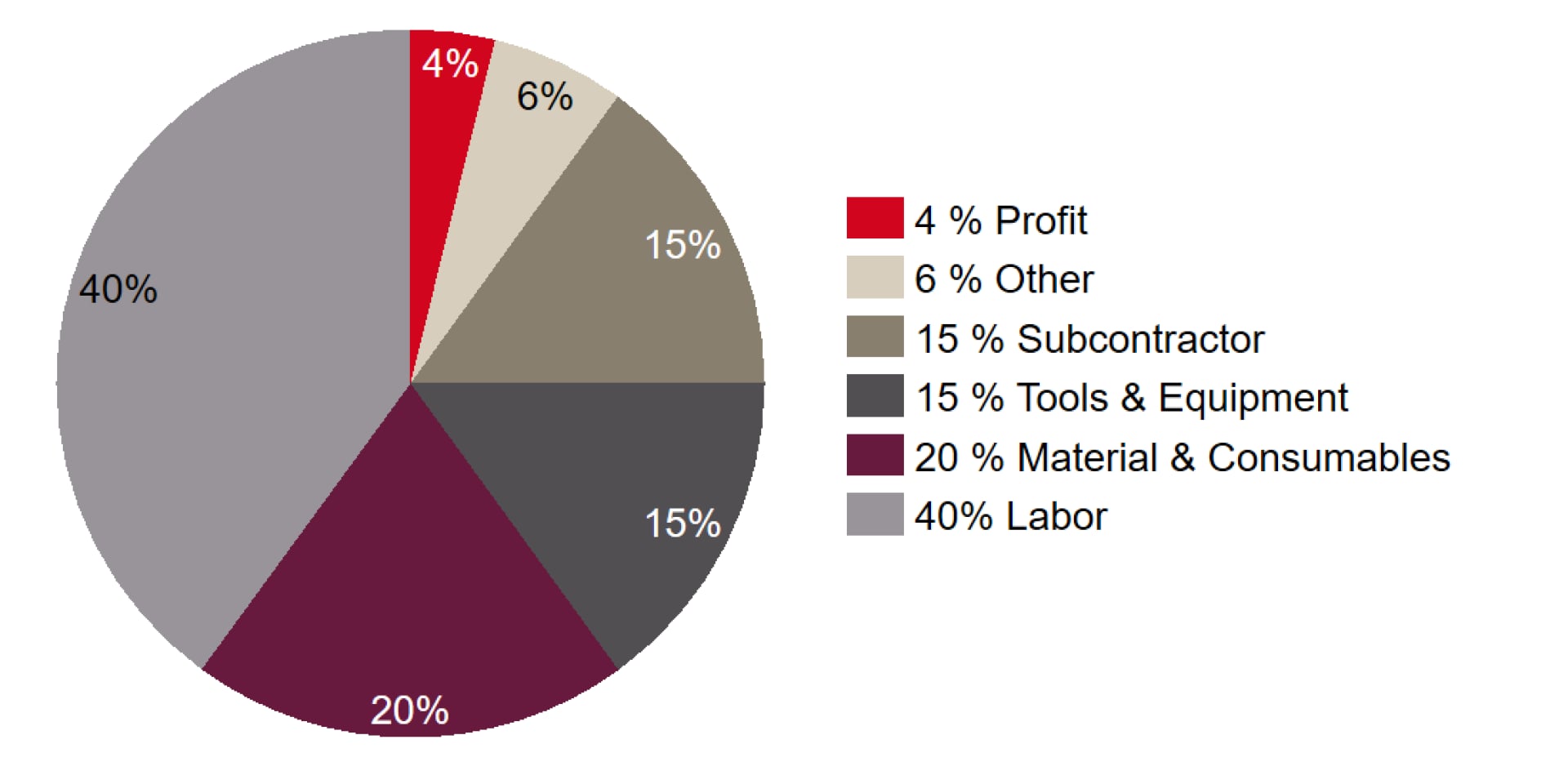
As shown in the examples above, a construction company with 30 employees can save between $100,000 and $250,000 per year if it switches to a suitable asset management solution.
Digital asset management doesn’t only make it easier to assign items to sites and workers, but it also saves you huge amounts of time as you can manage administrative assets much more easily.
Let’s see how.
Asset and employee-related document management
Ideally, you would work with an asset management software vendor to load your administrative assets onto the system. They might include:
- Health & Safety certification
- Employee certifications and training schedules
- Vehicle tax due dates
- Professional body membership details
- Rental equipment return dates
- Site cost allocations
You assign to each of these items dates when you need to take action, such as renewing certification or arranging fresh training. The employees responsible for action are sent automated reminders before the due dates, ensuring no business critical administration slips through the net.
As a result, you no longer have to spend large amounts of time monitoring administrative renewals. Automated reminders ensure that each task is assigned to the responsible individual in time. It is now simple to remain compliant with important issues like Health & Safety inspections and certification, meaning that you avoid the possibility of your cost centres being hit by major fines.
Again, Hilti has seen what savings can be made in the real world by digitising administrative assets.
- A company spending 20 hours per month administrating training certificates, work permits and safety data sheets can use digital asset management to slash this time by 33%.
- A firm spending four hours a month monitoring due dates can cut this time by 90% thanks to automated renewals offered by its digital asset management software.
Evaluating a digital asset management system
A good digital asset management system finally puts you in control of your physical assets such as tools, vehicles, equipment and consumables. When you are evaluating a system designed for the construction industry, you would typically be looking for the following features and capabilities.
- Robust asset identification. You need hardware that can be applied to all type of physical assets, allowing you and your workers to scan and track each item with your own smartphone. Ideally this would be a robust barcode, NFC or Bluetooth tag that can withstand rough handling and tough weather conditions.
- Flexible software. The software you use needs to be portable, so it can be used on-site and on the move. If it is cloud based, it will provide each user with real time information, and if it can be used on devices such as iOS and Android smartphones, it makes sourcing compatible hardware easier and doesn’t tie you into proprietary handsets. To minimise hassle and to give you peace of mind, it’s also wise to choose software that offers regular updates, strong data security and is compliant with data protection regulations.
- Service. Any system needs to be tailored to your own inventory and working practices, ideally with expert support from a vendor. This might include help with data upload, asset tagging and onsite training so you can implement the system as smoothly as possible.
- Reliable partner. There are many digital asset management software vendors out there, ranging from start-ups to long-established companies with a construction industry focus. When selecting a solution for your business, it’s wise to look for a partner with a record of continuously improving its software and which offers you expert advice and support – as and when you need it. Because you are making a long-term investment and commitment, you also need to be confident that your chosen vendor will remain in business for a long time. If a fledgling software company folds, then you will be on your own – with an expensive solution that is rapidly becoming obsolete.
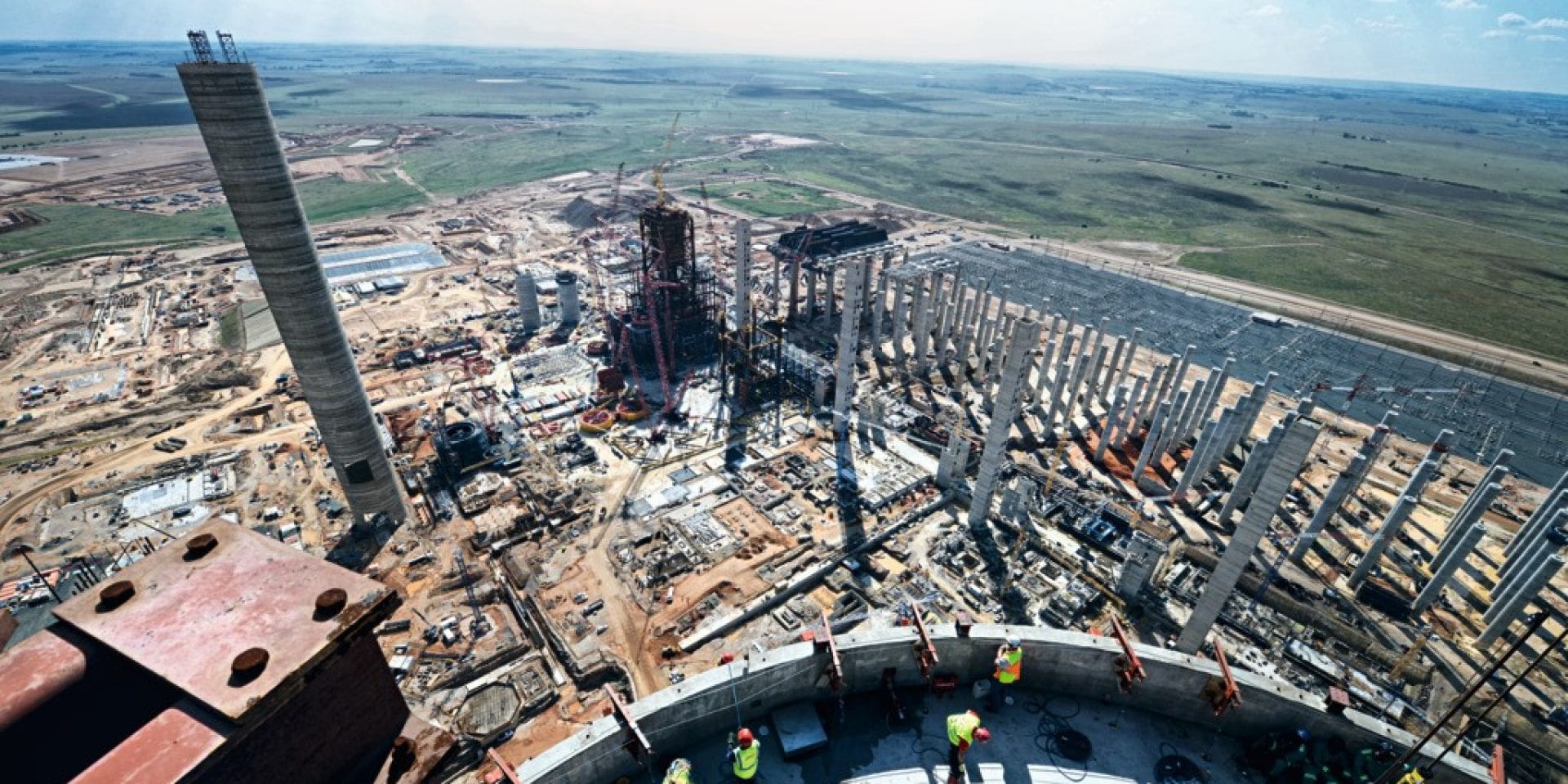
The business case for switching to digital asset management
Digital asset management software is increasingly easy to use and relatively cheap to implement. Importantly, cloud based platforms now keep your data more securely than ever. With the right choice of software and intelligent implementation, it will more than pay for itself very quickly – by cutting expenditure on physical assets, by freeing up staff time for more productive purposes, by eliminating delays on site and by reducing the likelihood of fines by accidentally failing to comply with regulations.
To learn more about how digital asset management can transform your construction business, please get in touch today.
Contact our customer service