- Home
- Company
- Media Relations
- Industry Blog
- Dust control
- 7 dust control methods for construction sites
7 dust control methods for construction sites
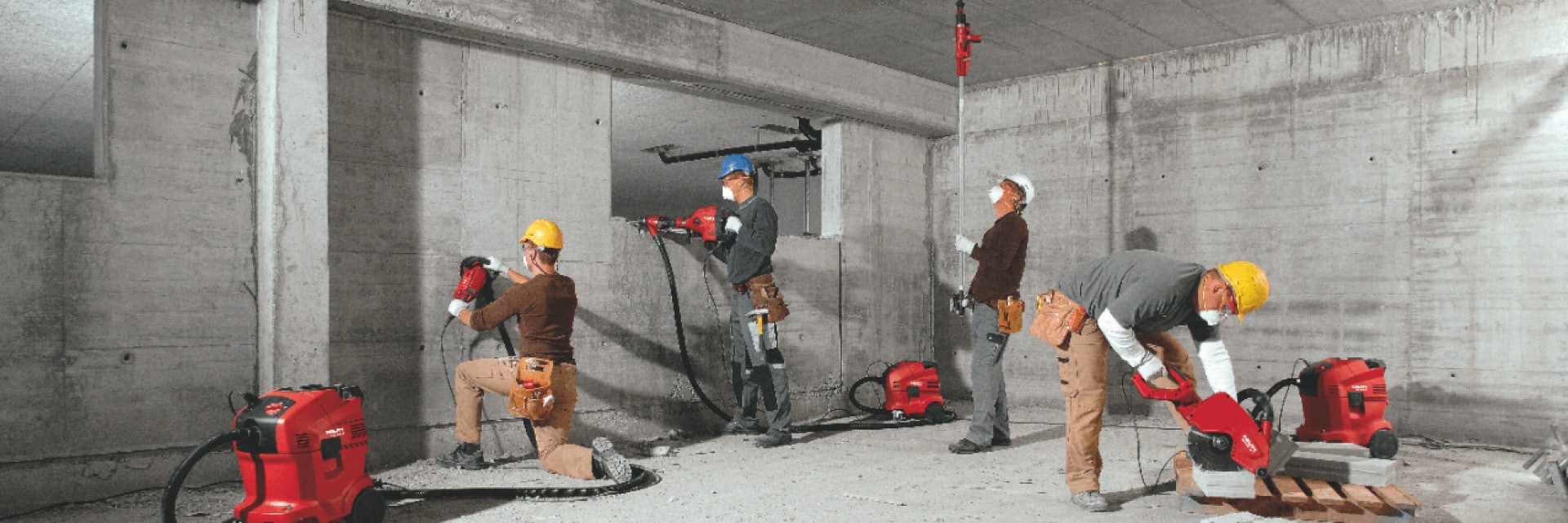
Wherever there's construction, there's dust. It's just part of the job. But RCS is extremely dangerous. This is because excessive exposure to RCS, over a period of time, can lead to reduced lung function and in the worst case, silicosis. Silicosis is the buildup of scar tissue in the lungs which hinder their ability to take in oxygen.
Exposure to this kind of hazardous substance must be prevented where practical, and when preventing exposure is impractical, then personal protective equipment (PPE) must be worn. This protection is all important in helping you avoid silicosis, which causes scar tissue to build up inside the lung and hinders its ability to take in oxygen.
It's in the best interest of everyone on site to ensure adequate preventative methods are taken. To help you achieve this, we've developed seven useful tools to manage the impact of RCS at your worksite.
Managing dust by elimination
1. Use cast-in anchor systems rather than post-installed
Cast-in anchor channels are the most ideal way to remove drilling from your installation process and subsequently avoid generating RCS dust at all. Whether for anchoring or rebar applications, our range of cast-in anchor products (both single point and channel options available as full systems) help you avoid dust generation without sacrificing on load capabilities.
Implementing dust control systems
2. Use Hilti's Dust Removal System (DRS) products
These attachable pieces of equipment serve the purpose of 'local exhaust ventilation'. They effectively get vacuum suction as close as possible to the working area to clear away dust.There are three ways you can take advantage of this, depending on the equipment you already have. Firstly, if you have a TE 4-A or TE 6-A cordless rotary hammer drill, these can be fitted with on-board powered dust hoods which act as mini-vacuum cleaners. Secondly, combi-hammers and breakers can be retrofitted with dust hoods that connect to vacuum cleaners. These include TE DRS-Y, TE DRS-M and TE DRS-B - click on model numbers to see which tools they are compatible with. Thirdly, in hammer-drilling applications you can use a hollow drill bit like the carbide tipped TE-CD or TE-YD, which connects to a vacuum cleaner and removes dust as you drill. Finally, you can re-equip yourself with appropriate tools compatible with our vacuum attachments.
3. Clean up with a vacuum instead of a broom
It can be very tempting to grab a broom to sweep up, and though this may appear to do the job, it's unlikely you'll manage to clean up every bit of a hazardous substance. Dust can get into cracks in the ground or be blown around by the wind, and then of course there is the difficult transition between floor and bin. A vacuum cleaner will ensure the safe removal of nearly every particle. You need to be thorough, but that's true for sweeping as well.
4. Don't use a compressed air gun
A compressed air gun will blow dust out of cracks and other hard to reach areas unlike a broom, but it won't do much for containment. Simply blowing hazardous dust like RCS away potentially does more harm than good. While it may get RCS out of your immediate vicinity, it will still be a hazard wherever it ends up. Compressed air guns are by all means a useful tool, but hazardous dust removal is not the right application. Some chemical anchor applications require the hole to be cleaned with a blast of compressed air though. In these cases, first suck all possible dust out with a vacuum cleaner and then be sure to use the correct PPE when cleaning the hole with compressed air.
5. Use shadow vacuuming techniques
By holding the nozzle of the vacuum cleaner close to your task, be it drilling, cutting, or grinding, you can extract dust as it's generated. Hilti vacuum cleaners feature consistently high suction to ensure that every particle gets caught. The VC 40-UM wet and dry vacuum cleaner has capacity to hold up to 40 kgs of dust, and its ability to become cordless means you can take it anywhere on site you need to go.
Employing dustless methodology
6. Use direct fastening instead of drilling and anchoring
In certain applications you'll be able to employ direct fastening methods. Rather than drilling and anchoring, you can fasten materials together gas-actuated or powder-actuated power load. When fasteners are driven in, the base material is displaced rather than removed. In this scenario, your fastenings are secure while no dust is generated.
7. Use wet coring with slurry collection instead of anchoring
With our DD-WMS 100 water management system, wet coring has never been easier. The constant flow of water absorbs waste particles (forming slurry) as you remove it from the base material, while the slurry is automatically taken care of. The recycling mode makes water usage extremely efficient. By collecting hazardous materials into a slurry, wet coring makes clean up far easier and disposal much safer.
Whichever method you decide will work best for you, make sure you use equipment according to instructions and follow best practice guidelines for design, specification and installation for all safety-critical applications.
For more information on dust prevention methods, or for a little bit of help deciding what will work for you, get in touch today.